PRODUCCIÓN Y GARANTIA DE CALIDAD SHOEI
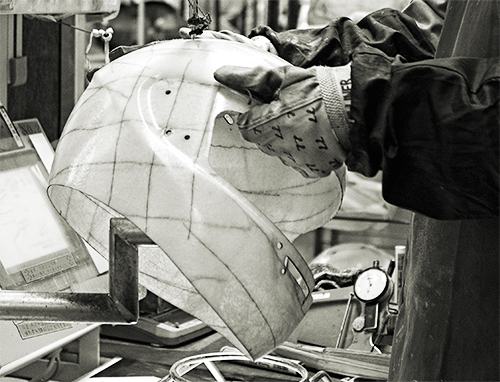
FABRICACIÓN DE LA CALOTA
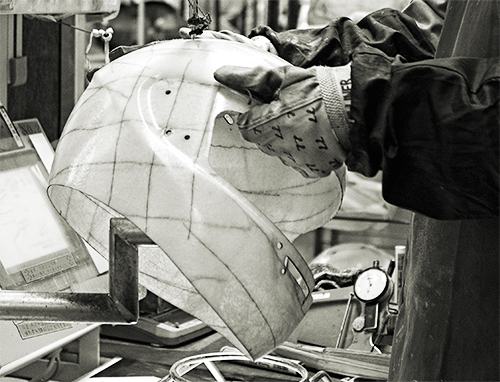
La tecnología patentada AIM y AIM+ de SHOEI integra una matriz multicapa de capas de fibra de vidrio entrelazadas a mano con fibras orgánicas y resina. Estos materiales se combinan de forma conjunta para maximizar la resistencia y la elasticidad en una calota muy resistente pero a su vez muy ligera. Cada capa está marcada personalmente por el técnico responsable de respaldar aún más la calidad de cada casco.
CORTE POR LÁSER
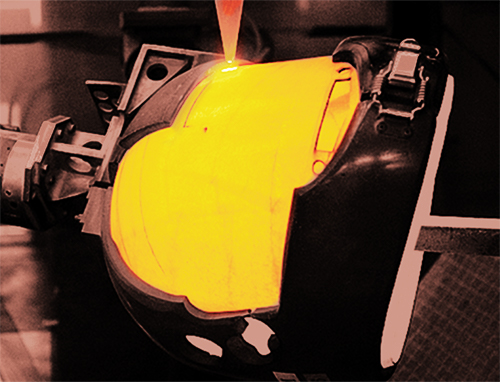
Los láseres controlados de forma robotizada le dan a cada casco su forma final al cortar las protuberancias creadas durante el proceso de moldeo de la calota, así como al crear las aberturas para los orificios de ventilación y área de visión. Una vez que se completa este proceso, todos los cascos se inspeccionan minuciosamente para garantizar un grosor y peso adecuado del material antes de pasar a la siguiente fase de fabricación.
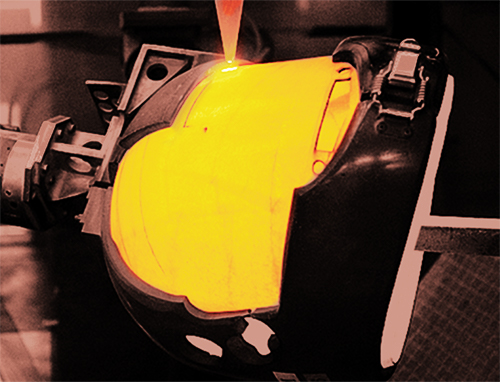
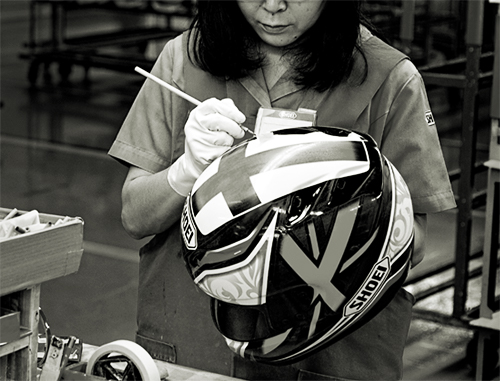
PINTURA Y APLICACIÓN DE GRÁFICAS
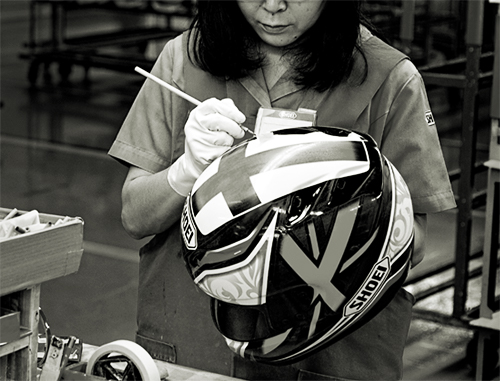
Los intrincados procedimientos de aplicación de gráficas y pintura de SHOEI son inigualables. Combinando trabajo hecho a mano con procesos de automatización de última generación para garantizar una calidad óptima, cada casco cuenta con un acabado de pintura de primera calidad y calcomanías aplicadas a mano antes de sellarse y protegerse con varias capas de lacado transparente. Todos y cada uno de los cascos SHOEI reciben hasta cinco capas de pintura antes del ensamblaje final.
AJUSTE Y CONFORT
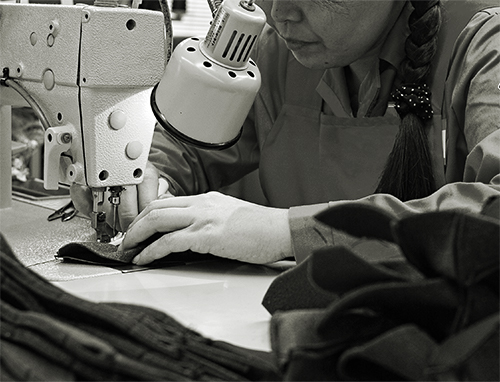
SHOEI sabe que un solo tamaño no sirve para todos y es por eso que ofrecemos varios tamaños de calota, algo que nos hace líderes en la industria, así como varios tamaños y espesores de acolchados interiores para garantizar un ajuste personalizable para todos y cada uno de los motoristas. Junto con una amplia investigación sobre formas y tamaños de cabeza, SHOEI incorpora una combinación de características exclusivas de comodidad y rendimiento en la construcción de cada casco. Componentes innovadores como nuestros acolchados interiores 3D Max-Dry, almohadillas centrales en 3D para encajar a la perfección con el contorno de la cabeza del motorista, acolchados totalmente desmontables, lavables y reemplazables, fabricación multicapa, canales para gafas y almohadillas para el cuello totalmente integradas acentúan la impecable y exclusiva comodidad que ofrece un casco SHOEI.
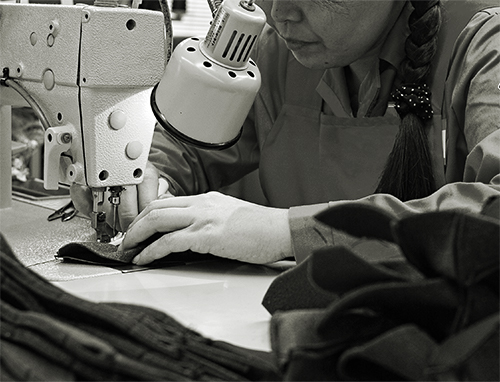
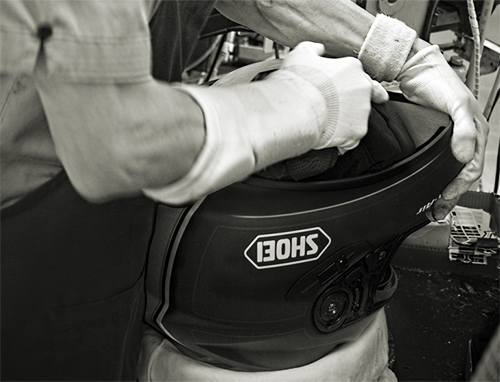
MONTAJE FINAL
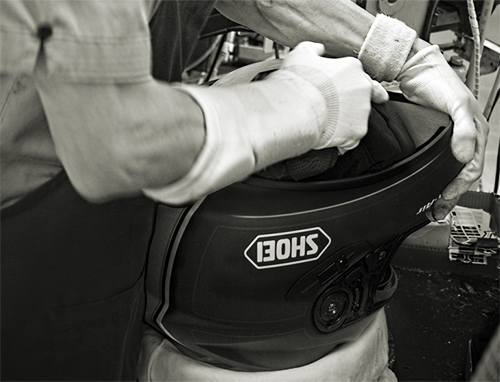
Un paso crítico en el proceso de fabricación, el ensamblaje final del casco se realiza con cuidado y precisión, incluida la instalación de mecanismos de ventilación, sellos de protección, EPS y acolchados interiores. Cada casco pasa una detallada inspección final antes de ser suministrado al usuario final. Este estricto cumplimiento de los procesos de producción y los estándares de control de calidad garantizan la alta calidad de un casco SHOEI.
EL TRABAJO MANUAL MARCA LA DIFERENCIA
El trabajo manual juega un papel significante en la fabricación de los cascos SHOEI. Esto se nota especialmente en el proceso de pintado.
IMPRIMACIÓN
Una vez que el casco se ha retirado del molde y se han eliminado todas las partes sobrantes y se han realizado las aperturas por láser, al casco se le aplica la primera capa de imprimación. A continuación, cada casco se limpia, lija y se pule a mano y con máquina obteniendo una superficie impecable para las posteriores operaciones de pintura. Trabajar las diferentes calotas de casco con sus propias particularidades requiere un alto grado de experiencia.
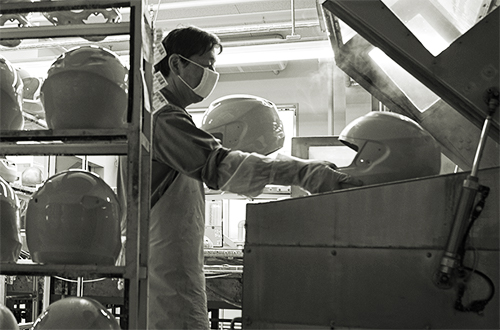
COMPROBACIÓN DE LA IMPRIMACIÓN
La imprimación del casco es cuidadosamente revisada por múltiples técnicos para detectar pequeñas imperfecciones. Posteriormente se pasa al proceso de pintado pero solamente si la superficie del casco es absolutamente perfecta.
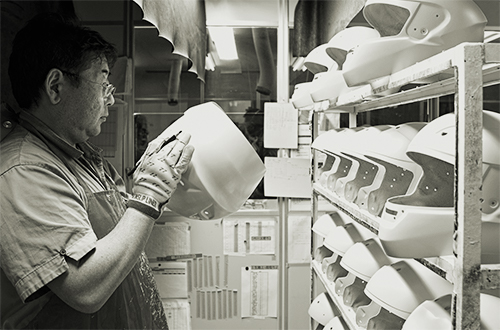
PINTURA
La calidad del proceso de pintado depende de la calidad y experiencia de cada pintor. Es prácticamente imposible aplicar una capa de pintura de alta calidad mediante una máquina, incluso con las última tecnología y pinturas de poliuretano. Por esta razón, solo técnicos especialmente calificados se encargan de llevar a cabo esta tarea.
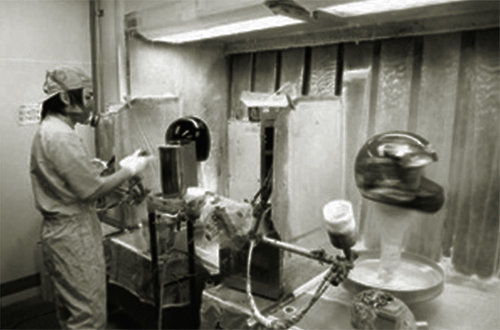
COMPROBACIÓN DE LA PINTURA
La pintura se somete a una minuciosa inspección en busca de posibles goteos e irregularidades antes que la calota del casco pase al siguiente proceso.
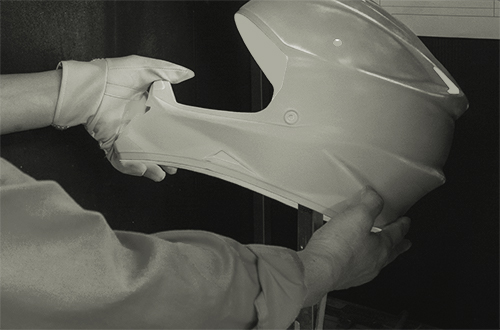
APLICACIÓN DE LAS GRÁFICAS
Diseños elaborados, extremadamente detallados y espectaculares son parte de la imagen de marca de un casco SHOEI. Es una etapa del proceso de trabajo muy difícil, las calcomanías al agua se aplican a mano por técnicos especialmente capacitados para finalizar el proceso de pintado del casco.
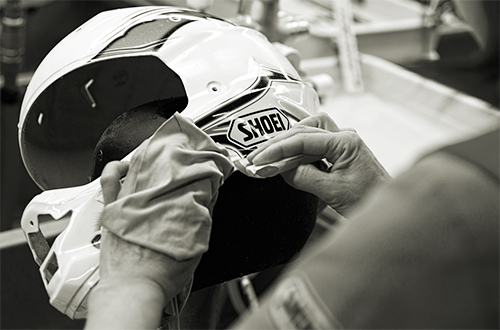
BARNIZ DE PROTECCIÓN
El último paso en el proceso de pintado es la aplicación a la calota de un barniz protector transparente para proteger la decoración y darle al casco su brillo SHOEI inconfundible.
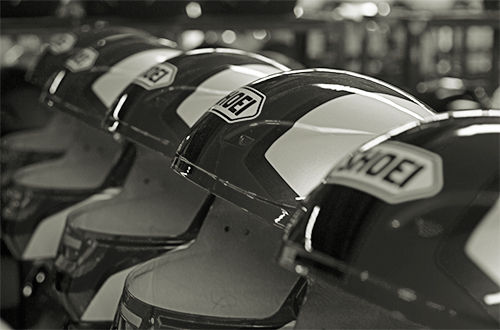
COMPROBACIÓN FINAL
Antes de realizar el montaje final, se inspecciona minuciosamente el acabado de pintado. La perfección, incluso en zonas poco visibles es imprescindible.
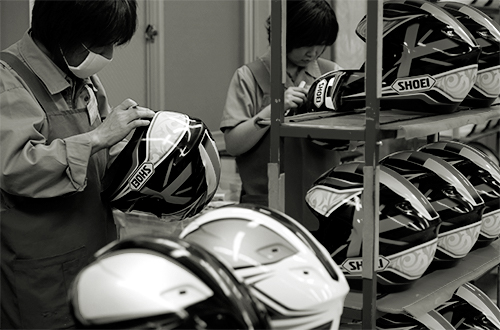
MAXIMA CALIDAD INCLUSO EN ZONAS INVISIBLES
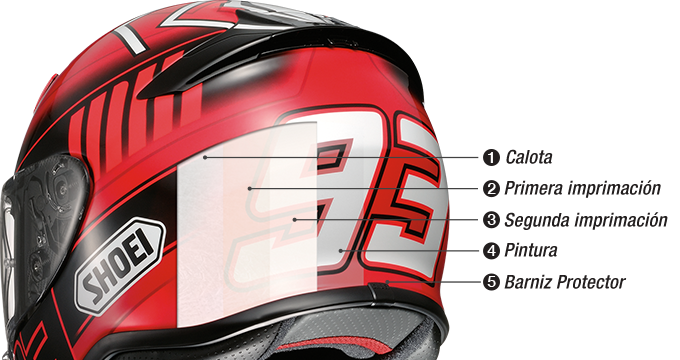
CONTROL DE CALIDAD
No solo invertimos toda nuestra energía y pasión en el diseño y el desarrollo de un producto, también un especial cuidado con cada casco durante el proceso de producción. Una serie de procesos únicos y vanguardistas se combinan para ofrecer la calidad sin igual por la que se conocen los cascos SHOEI. Además, cada casco debe pasar rigurosas inspecciones durante todo el proceso de producción antes de ser premiado con el famoso hexágono de SHOEI.
CONTROL DE CALIDAD DURANTE EL DESARROLLO
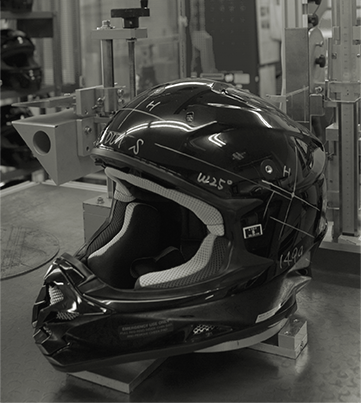
Las normas de seguridad específicas de cada país juegan el papel más importante durante el desarrollo de un casco. La calota y el EPS son sometidas a diferentes pruebas de dureza y elasticidad modificándose según sea necesario. Esto se traduce en un casco que cumpla con las estrictas normas que se aplican combinado con todas las ventajas del diseño original.
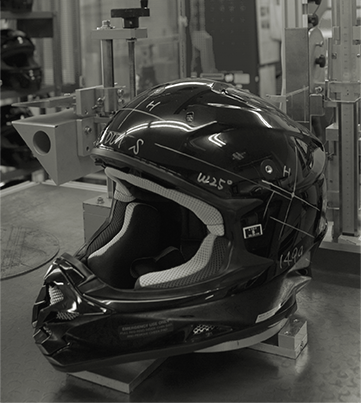
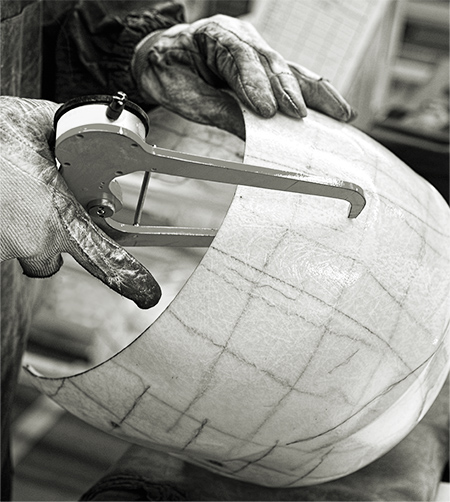
CONTROL DE CALIDAD DURANTE LA PRODUCCIÓN
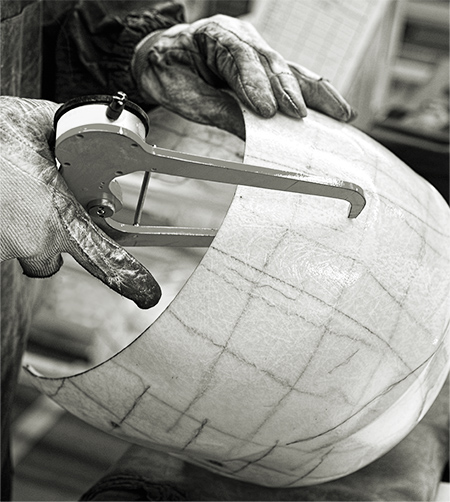
SHOEI realiza estrictos controles de calidad en todas sus fases de fabricación. Desde la fabricación de la calota hasta el montaje final. Además, se toman muestras regularmente de la producción normal y son comprobadas en las instalaciones de la propia compañía. Cada año más de 3000 cascos se comprueban para asegurar una seguridad perfecta y luego son destruidos. Estos cascos de prueba son una gran contribución a la seguridad general que se ofrece en nuestros productos.